Additive Manufacturing Services
In our pursuit of excellence, Alphaden Energy has embraced additive manufacturing services. Our in-house 3D printing capabilities allow us to create customized parts and tools with speed and precision. Whether it's producing spare components for critical equipment or developing rapid prototypes for new drilling technologies, we harness additive manufacturing for innovation and efficiency.
OUR ADDITIVE MANUFACTURING CAPABILITIES
Alphaden has partnered with Sciaky & Famaero, offering the largest, fully-programmable means of achieving near-net shape parts made of:Titanium and Titanium Alloys, Inconel 600, 625, 718, Nickel and Copper Nickel Alloys, Stainless Steels 300 Series, Alloy Steels, Cobalt Alloys, 4130 Steel, Zircalloy, Tantalum, Tungsten, Niobium, Molybdenum, And many more! Any material weldable to itself and available in wire is open for discussion.
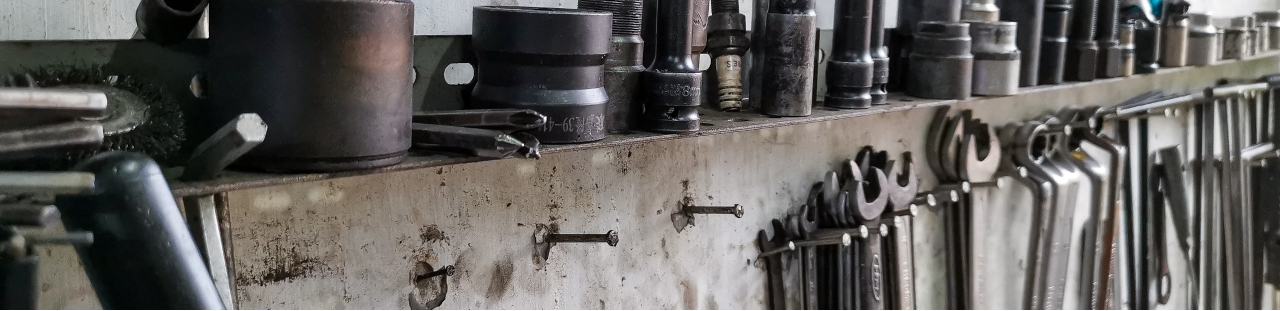
Electron Beam Additive Manufacturing (EBAM) ®
Sciaky's exclusive Electron Beam Additive Manufacturing (EBAM®) process employs wire feedstock and an electron beam heat source within a vacuum chamber to craft near-net-shaped components. Beginning with a 3D CAD model converted to CNC code, the electron beam gun incrementally deposits metal layers until reaching the near-net shape. Subsequently, the part undergoes final heat treatment and machining.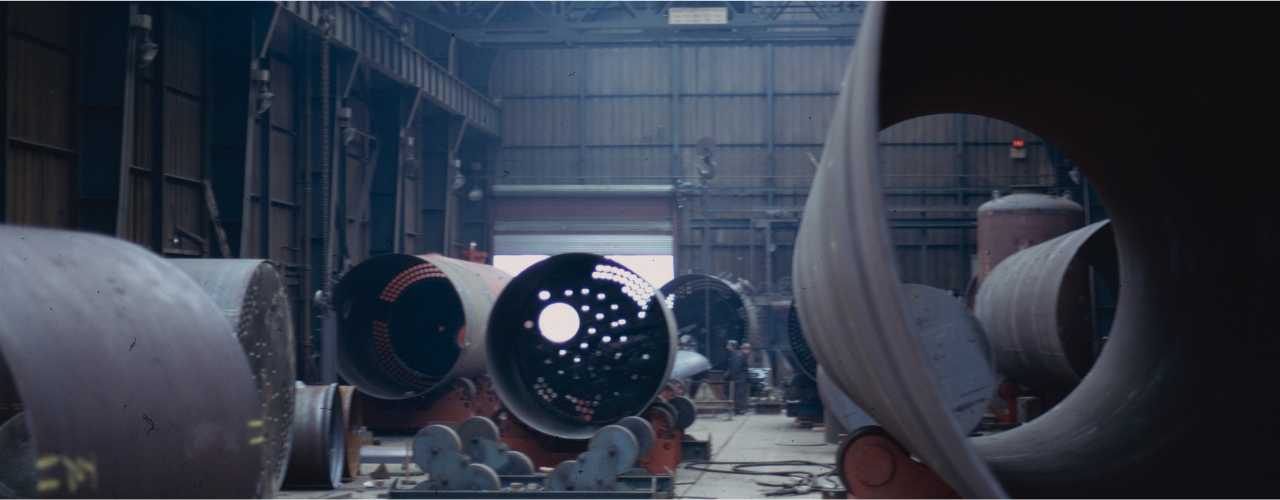
This versatile process accommodates components of varying sizes, constrained solely by the vacuum chamber's dimensions, and the Electron Beam (EB) serves as the energy source, melting wire feedstock and adding layers to achieve the desired geometry, facilitating the creation of new components, incorporation of features, or repair of parts.
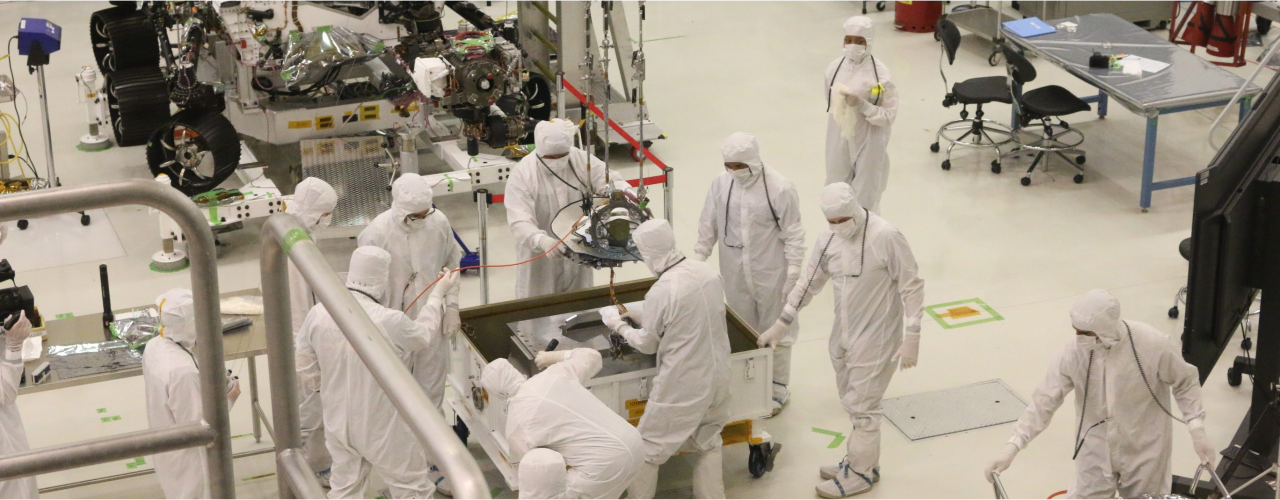
A closed-loop control technology that provides real-time adaptive control
The capability to achieve predictable and repeatable operations is important for wirefeed AM, and this is needed to increase the stability of the deposition process.Sciaky offers the only real-time adaptive control system in the market that can sense and digitally self-adjust metal deposition with precision and repeatability, named the IRISS® Interlayer Realtime Imaging & Sensing System.
• Digital parameter control and adjustments are made in response to real-time measured data, without process disruption.
• Records every second of deposition, so the entire build can be reviewed, verifying consistency and keeping a record for later review.
• Prevents surprises by dynamically adjusting parameters to maintain part integrity.
• Better insures net shape fabrication and reduces post processing time and costs such as machining and inspection
Technological ADVANTAGES we offer:
In addition to Accelerated lead times, cost-efficiency, ability to manufacture materials for use in the harshest environmental conditions, and reliability during temporary shutdowns, turnaround maintenance (TAM), pit stops, or addressing spare parts availability,• EBAM boasts impressive deposition rates, spanning from 7 to 25 lbs. (3.18 to 11.34 kg) of metal per hour, rendering it the fastest metal additive manufacturing process available.
• The IRISS process control effectively eradicates inconsistencies from the initial to the final layer and adjustments are executed in response to real-time data without disrupting the process.
• As an illustration, AM-grade Titanium 6AI-4V powder costs approximately 141% more than Titanium 6AI-4V wire on average, with Titanium wire offering quicker turnaround times, at times up to 4 weeks faster. Notably, AM-grade Stainless Steel 316 powder typically carry twice the average cost of their wire counterparts.
• Plus, with an EBAM dual wirefeed system, you can combine two different metal alloys into a single melt pool, to create “custom alloy” parts or ingots. You also have the option to change the mixture ratio of the two materials. These unique benefits are exclusive to the EBAM dual wirefeed process and are not available with any other metal AM process in the market.